Linije za ubrizgavanje hemikalija u bušotini – zašto pokvare?Iskustva, izazovi i primjena novih metoda ispitivanja
Autorska prava 2012, Društvo inženjera nafte
Abstract
Statoil posluje na nekoliko polja na kojima se primjenjuje kontinuirano ubrizgavanje inhibitora kamenca u bušotinu.Cilj je zaštititi gornju cijev i sigurnosni ventil od (Ba/Sr) SO4 ili CaCO;razmjera, u slučajevima kada je cijeđenje kamenca teško i skupo za redovno obavljanje, npr. uvezivanje podmorskih polja.
Kontinuirano ubrizgavanje inhibitora kamenca u bušotinu je tehnički prikladno rješenje za zaštitu gornje cijevi i sigurnosnog ventila u bušotinama koje imaju potencijal stvaranja kamenca iznad proizvodnog pakera;posebno u bušotinama koje nije potrebno redovno istiskivati zbog potencijala stvaranja kamenca u blizini bušotine.
Projektovanje, rad i održavanje linija za ubrizgavanje hemikalija zahtevaju dodatni fokus na odabir materijala, hemijsku kvalifikaciju i praćenje.Pritisak, temperatura, režimi protoka i geometrija sistema mogu predstavljati izazove za siguran rad.Izazovi su identificirani u nekoliko kilometara dugim linijama za injektiranje od proizvodnog pogona do podmorskog šablona iu injekcionim ventilima dolje u bušotinama.
Razmatrana su terenska iskustva koja pokazuju složenost sistema kontinuiranog ubrizgavanja u bušotini u pogledu padavina i korozije.Zastupljene su laboratorijske studije i primjena novih metoda za hemijsku kvalifikaciju.Potrebe za multidisciplinarnim akcijama su adresirane.
Uvod
Statoil posluje na nekoliko polja na kojima je primijenjeno kontinuirano ubrizgavanje hemikalija u bušotinu.Ovo uglavnom uključuje ubrizgavanje inhibitora kamenca (SI) gdje je cilj zaštita gornjeg cijevi i sigurnosnog ventila u bušotini (DHSV) od (Ba/Sr) SO4 ili CaCO;skala.U nekim slučajevima razbijač emulzije se ubrizgava niz bušotinu kako bi započeo proces separacije što je moguće dublje u bušotini na relativno visokoj temperaturi.
Kontinuirano ubrizgavanje inhibitora kamenca u nizu je tehnički prikladno rješenje za zaštitu gornjeg dijela bušotina koje imaju potencijal skaliranja iznad proizvodnog pakera.Kontinuirano ubrizgavanje se može preporučiti posebno u bušotinama koje nije potrebno istiskivati zbog niskog potencijala stvaranja kamenca u blizini bušotine;ili u slučajevima kada je cijeđenje kamenca teško i skupo za redovno obavljanje, npr. uvezivanje podmorskih polja.
Statoil ima prošireno iskustvo u kontinuiranom ubrizgavanju hemikalija u gornje sisteme i podmorske šablone, ali novi izazov je da se tačka ubrizgavanja dalje duboko u bušotinu.Projektovanje, rad i održavanje linija za ubrizgavanje hemikalija zahteva dodatni fokus na nekoliko tema;kao što su odabir materijala, hemijska kvalifikacija i praćenje.Pritisak, temperatura, režimi protoka i geometrija sistema mogu predstavljati izazove za siguran rad.Identificirani su izazovi u dugim (nekoliko kilometara) linijama za injektiranje od proizvodnog pogona do podmorskog šablona i u injekcione ventile dolje u bušotinama;Fig.1.Neki od sistema za ubrizgavanje su radili po planu, dok su drugi otkazali iz raznih razloga.Planirano je nekoliko novih terenskih razvoja za ubrizgavanje hemikalija u bušotinu (DHCI);kako god;u nekim slučajevima oprema još nije u potpunosti osposobljena.
Primjena DHCI je složen zadatak.Uključuje završetak i dizajn bunara, hemiju bunara, sistem gornje strane i sistem doziranja hemikalija gornjeg procesa.Hemikalija će se pumpati sa gornje strane preko linije za ubrizgavanje hemikalija do opreme za završetak i dole u bunar.Stoga je u planiranju i realizaciji ove vrste projekta saradnja više disciplina ključna.Moraju se procijeniti različita razmatranja i važna je dobra komunikacija tokom dizajna.Uključeni su procesni inženjeri, podmorski inženjeri i inženjeri za završetak radova koji se bave temama hemije bunara, odabira materijala, osiguranja protoka i upravljanja proizvodnim hemikalijama.Izazovi mogu biti hemijski top ili temperaturna stabilnost, korozija i u nekim slučajevima efekat vakuuma zbog lokalnog pritiska i efekata protoka u liniji za ubrizgavanje hemikalija.Pored ovih, uslovi kao što su visoki pritisak, visoka temperatura, visoka brzina gasa, visok potencijal skaliranja,Pupčana i duboka tačka ubrizgavanja na velike udaljenosti u bušotini, postavljaju različite tehničke izazove i zahtjeve za ubrizganu hemikaliju i ventil za injektiranje.
Pregled DHCI sistema instaliranih u Statoil operacijama pokazuje da iskustvo nije uvijek bilo uspješno. Tabela 1. Međutim, planiranje za poboljšanje dizajna ubrizgavanja, hemijske kvalifikacije, rada i održavanja je u toku.Izazovi se razlikuju od polja do polja, a problem nije nužno u tome što sam ventil za ubrizgavanje kemikalija ne radi.
Proteklih godina naišlo se na nekoliko izazova vezanih za linije za ubrizgavanje kemikalija u bušotini.U ovom radu su dati neki primjeri iz ovih iskustava.U radu se razmatraju izazovi i mjere koje se poduzimaju za rješavanje problema vezanih za DHCI linije.Date su dvije istorije slučajeva;jedan o koroziji i jedan o kraljevu hemijskog oružja.Razmatrana su terenska iskustva koja pokazuju složenost sistema kontinuiranog ubrizgavanja u bušotini u pogledu padavina i korozije.
Razmatraju se i laboratorijske studije i primjena novih metoda za hemijsku kvalifikaciju;kako pumpati hemikaliju, potencijal za stvaranje kamenca i prevenciju, primjenu složene opreme i kako će hemikalija uticati na gornji sistem kada se hemikalija ponovo proizvodi.Kriterijumi prihvatljivosti za primenu hemikalija uključuju pitanja životne sredine, efikasnost, kapacitet skladištenja na vrhu, brzinu pumpe, da li se postojeća pumpa može koristiti itd. Tehničke preporuke moraju biti zasnovane na kompatibilnosti fluida i hemije, detekcije ostataka, kompatibilnosti materijala, podmorskog dizajna pupčanika, sistema doziranja hemikalija i materijala u okruženju ovih linija.Hemikalija se možda mora inhibirati hidratima kako bi se spriječilo začepljenje linije za ubrizgavanje zbog invazije plina i hemikalija se ne smije smrzavati tokom transporta i skladištenja.U postojećim internim smjernicama postoji lista za provjeru koje hemikalije se mogu primijeniti u svakoj tački sistema. Fizička svojstva kao što je viskoznost su važna.Sistem injektiranja može podrazumijevati 3-50 km udaljenosti pupčane podmorske protočne linije i 1-3 km dolje u bunar.Stoga je temperaturna stabilnost takođe važna.Procjena efekata nizvodno, npr. u rafinerijama, također može biti uzeta u obzir.
Sistemi za ubrizgavanje hemikalija u bušotini
Isplativost
Kontinuirano ubrizgavanje inhibitora kamenca u bušotinu radi zaštite DHS-a ili proizvodnih cijevi može biti isplativo u poređenju sa stiskanjem bušotine inhibitorom kamenca.Ova aplikacija smanjuje potencijal za oštećenje formacije u poređenju sa tretmanima stiskanjem kamenca, smanjuje mogućnost problema u procesu nakon istiskivanja kamenca i daje mogućnost kontrole brzine ubrizgavanja hemikalija iz sistema za injektiranje na vrhu.Sistem za injektiranje se takođe može koristiti za kontinuirano ubrizgavanje drugih hemikalija u bušotinu i na taj način može smanjiti druge izazove koji se mogu pojaviti dalje nizvodno od procesnog postrojenja.
Izvršena je sveobuhvatna studija za razvoj strategije dobošnog polja Oseberg S ili polja.Najveći problem bio je CaCO;stvaranje kamenca u gornjoj cijevi i mogući kvar DHSV-a.Oseberg S ili razmatranja strategije upravljanja kamencem su zaključili da je tokom perioda od tri godine, DHCI bio najefikasnije rješenje u bušotinama u kojima su funkcionisale linije za ubrizgavanje hemikalija.Glavni element troškova u odnosu na konkurentnu tehniku istiskivanja kamenca bila je odložena nafta, a ne hemijski/operativni troškovi.Za primenu inhibitora kamenca u gas liftu, glavni faktor na cenu hemikalije bila je visoka brzina dizanja gasa koja je dovela do visoke koncentracije SI, pošto je koncentracija morala biti uravnotežena sa brzinom dizanja gasa kako bi se izbegao hemijski king.Za dva bunara na Oseberg S ili koji su imali dobro funkcionišuće linije DHC I, ova opcija je izabrana da zaštiti DHS V od CaCO;skaliranje.
Sistem kontinuiranog ubrizgavanja i ventili
Postojeća rješenja za završetak koji koriste sustave za kontinuirano ubrizgavanje kemikalija suočavaju se s izazovima u sprječavanju začepljenja kapilarnih vodova.Obično se sistem za ubrizgavanje sastoji od kapilarnog voda, 1/4” ili 3/8” vanjskog prečnika (OD), spojenog na površinski razvodnik, napajanog kroz i spojenog na vješalicu cijevi na prstenastoj strani cijevi.Kapilarna linija je pričvršćena na vanjski prečnik proizvodne cijevi pomoću specijalnih obujmica za cijevi i prolazi na vanjskoj strani cijevi sve do injektora za kemijsko ubrizgavanje.Trn se tradicionalno postavlja uzvodno od DHS V ili dublje u bušotinu s namjerom da se ubrizganoj hemikaliji da dovoljno vremena za disperziju i da se hemikalija smjesti tamo gdje su izazovi pronađeni.
Na ventilu za ubrizgavanje hemikalija, slika 2, mali uložak prečnika oko 1,5” sadrži nepovratne ventile koji sprečavaju da tečnosti iz bušotine uđu u kapilarnu liniju.To je jednostavno mala lutka koja jaše na oprugu.Sila opruge postavlja i predviđa pritisak koji je potreban da bi se otvorio klin sa zaptivnog sjedišta.Kada hemikalija počne da teče, kuka se podiže sa svog sedišta i otvara nepovratni ventil.
Potrebno je imati instalirana dva nepovratna ventila.Jedan ventil je primarna barijera koja sprečava da tečnosti iz bušotine uđu u kapilarnu liniju.Ovo ima relativno nizak pritisak otvaranja (2-15 bara). Ako je hidrostatički pritisak unutar kapilarne linije manji od pritiska u bušotini, fluidi iz bušotine će pokušati da uđu u kapilarni vod.Drugi nepovratni ventil ima netipičan pritisak otvaranja od 130-250 bara i poznat je kao sistem prevencije U-cijev.Ovaj ventil sprečava da hemikalija unutar kapilarnog voda slobodno teče u bušotinu ako hidrostatički pritisak unutar kapilarne linije bude veći od pritiska u bušotini na mestu ubrizgavanja hemikalije unutar proizvodnog cjevovoda.
Pored dva nepovratna ventila, obično postoji i in-line filter, svrha ovoga je da osigura da nikakvi ostaci bilo koje vrste ne mogu ugroziti sposobnost zaptivanja sistema nepovratnih ventila.
Dimenzije opisanih nepovratnih ventila su prilično male, a čistoća ubrizganog fluida je neophodna za njihovu operativnu funkcionalnost.Vjeruje se da se ostaci iz sistema mogu isprati povećanjem protoka unutar kapilarne linije, tako da se nepovratni ventili namjerno otvaraju.
Kada se nepovratni ventil otvori, protok protoka se brzo smanjuje i širi se kapilarnom linijom dok se pritisak ponovo ne poveća.Povratni ventil će se tada zatvoriti sve dok protok hemikalija ne stvori dovoljan pritisak da otvori ventil;rezultat su oscilacije pritiska u sistemu nepovratnih ventila.Što veći pritisak otvaranja ima sistem nepovratnog ventila, to je manja površina protoka uspostavljena kada se nepovratni ventil otvori i sistem pokušava da postigne ravnotežne uslove.
Ventili za ubrizgavanje hemikalija imaju relativno nizak pritisak otvaranja;i ako pritisak u cevi na ulaznoj tački hemikalije postane manji od zbira hidrostatskog pritiska hemikalija unutar kapilarnog voda plus pritisak otvaranja nepovratnog ventila, u gornjem delu kapilarne linije će se pojaviti blizu vakuuma ili vakuuma.Kada se ubrizgavanje hemikalije zaustavi ili je protok hemikalije nizak, u gornjem delu kapilarne linije počeće da se javljaju uslovi blizu vakuuma.
Nivo vakuuma zavisi od pritiska u bušotini, specifične težine ubrizgane hemijske smeše koja se koristi unutar kapilarnog voda, pritiska otvaranja nepovratnog ventila na mestu ubrizgavanja i protoka hemikalije unutar kapilarne linije.Uslovi u bušotini će varirati tokom životnog veka polja i potencijal za vakuum će se, stoga, takođe menjati tokom vremena.Važno je biti svjestan ove situacije kako biste pravilno razmotrili i preduzeli mjere opreza prije nego što se pojave očekivani izazovi.
Zajedno sa niskim stopama ubrizgavanja, obično rastvarači koji se koriste u ovim vrstama aplikacija isparavaju uzrokujući efekte koji nisu u potpunosti istraženi.Ovi efekti su gun king ili taloženje čvrstih materija, na primjer polimera, kada rastvarač isparava.
Dalje, galvanske ćelije se mogu formirati u prelaznoj fazi između tečne površine hemikalije i gasne faze ispunjene parom iznad.To može dovesti do lokalne pitting korozije unutar kapilarne linije kao rezultat povećane agresivnosti kemikalije u ovim uvjetima.Pahuljice ili kristali soli koji se formiraju kao film unutar kapilarne linije kako se njena unutrašnjost suši mogu zaglaviti ili začepiti kapilarnu liniju.
Pa barijerna filozofija
Prilikom projektovanja robusnih bunara, Statoil zahteva da sigurnost bušotine bude na mestu u svakom trenutku tokom životnog ciklusa bunara.Stoga, Statoil zahtijeva da postoje dvije nezavisne barijere za bunar netaknute.Slika 3 prikazuje šemu atipične barijere bunara, gdje plava boja predstavlja primarni omotač barijere bunara;u ovom slučaju proizvodne cijevi.Crvena boja predstavlja omotač sekundarne barijere;kućište.Na lijevoj strani skice ubrizgavanje kemikalije je označeno kao crna linija s točkom ubrizgavanja u proizvodnu cijev u području označenom crvenom (sekundarna barijera).Uvođenjem sistema za injektiranje hemikalija u bušotinu ugrožavaju se i primarna i sekundarna barijera bušotine.
Istorijat slučaja korozije
Redoslijed događaja
Hemijsko ubrizgavanje inhibitora kamenca u bušotinu primijenjeno je u naftno polje kojim upravlja Statoil na norveškom kontinentalnom pojasu.U ovom slučaju primijenjeni inhibitor kamenca je prvobitno bio kvalificiran za primjenu na površini i podmorju.Nakon ponovnog završetka bušotine uslijedila je ugradnja DHCIpointat2446mMD, sl.3.Ubrizgavanje inhibitora gornjeg kamenca na dnu bušotine započeto je bez daljeg ispitivanja hemikalije.
Nakon godinu dana rada uočena su curenja u sistemu za ubrizgavanje hemikalija i započeta su istraživanja.Curenje je imalo štetan uticaj na barijere bunara.Slični događaji su se desili za nekoliko bunara i neke od njih su morale biti zatvorene dok je istraga bila u toku.
Proizvodne cijevi su izvučene i detaljno proučene.Napad korozije bio je ograničen na jednu stranu cijevi, a neki spojevi cijevi su bili toliko korodirani da je kroz njih zapravo bilo rupa.Otprilike 8,5 mm debljine 3% hromiranog čelika se raspao za manje od 8 mjeseci.Glavna korozija se dogodila u gornjem dijelu bušotine, od glave bunara do otprilike 380 m MD, a najgore korodirani spojevi cijevi pronađeni su na oko 350 m MD.Ispod ove dubine uočena je mala ili nikakva korozija, ali je pronađeno mnogo krhotina na OD cijevi.
Kućište od 9-5/8'' je također izrezano i izvučeno i uočeni su slični efekti;sa korozijom u gornjem dijelu bunara samo s jedne strane.Inducirano curenje je uzrokovano pucanjem oslabljenog dijela kućišta.
Materijal linije za ubrizgavanje hemikalija bila je legura 825.
Hemijska kvalifikacija
Hemijska svojstva i ispitivanje korozije su važni fokusi u kvalifikaciji inhibitora kamenca, a stvarni inhibitor kamenca je kvalificiran i korišten u površinskim i podmorskim aplikacijama nekoliko godina.Razlog za primjenu stvarne hemikalije na nižoj bušotini bila su poboljšana svojstva okoliša zamjenom postojeće hemikalije u bušotini. Međutim, inhibitor kamenca se koristio samo pri temperaturama na vrhu i morskom dnu (4-20℃).Kada se ubrizgava u bunar, temperatura hemikalije je mogla biti i do 90℃, ali na ovoj temperaturi nisu vršena daljnja ispitivanja.
Inicijalne testove korozivnosti izvršio je dobavljač hemikalije i rezultati su pokazali 2-4 mm/godišnje za ugljenični čelik na visokoj temperaturi.Tokom ove faze bilo je minimalno angažovanje materijalno-tehničke kompetencije operatera.Operater je kasnije izvršio nove testove koji su pokazali da je inhibitor kamenca bio vrlo korozivan za materijale u proizvodnim cijevima i proizvodnom kućištu, sa stopama korozije preko 70 mm/godišnje.Materijal linije za hemijsko ubrizgavanje Alloy 825 nije testiran na inhibitor kamenca prije ubrizgavanja.Temperatura u bušotini može doseći 90℃ i u ovim uslovima je trebalo izvršiti odgovarajuća ispitivanja.
Istraživanje je takođe otkrilo da je inhibitor kamenca kao koncentrirani rastvor prijavio pH <3,0.Međutim, pH nije izmjeren.Kasnije je izmjereni pH pokazao vrlo nisku vrijednost pH 0-1.Ovo ilustruje potrebu za mjerenjima i razmatranjem materijala pored datih pH vrijednosti.
Interpretacija rezultata
Linija za ubrizgavanje (Sl.3) je konstruisana tako da daje hidrostatički pritisak inhibitora kamenca koji premašuje pritisak u bušotini na mestu injektiranja.Inhibitor se ubrizgava pod većim pritiskom nego što postoji u bušotini.Ovo rezultira efektom U-cijevi pri zatvaranju bunara.Ventil će se uvijek otvoriti s većim pritiskom u liniji za ubrizgavanje nego u bušotini.Stoga može doći do vakuuma ili isparavanja u liniji za ubrizgavanje.Brzina korozije i rizik od taloženja je najveći u zoni tranzicije gas/tečnost zbog isparavanja rastvarača.Laboratorijski eksperimenti izvedeni na kuponima potvrdili su ovu teoriju.U bušotinama u kojima je došlo do curenja, sve rupe u injekcionim vodovima bile su locirane u gornjem delu linije za ubrizgavanje hemikalija.
Slika 4 prikazuje fotografiju DHC I linije sa značajnom pitting korozijom.Korozija uočena na vanjskoj cijevi za proizvodnju ukazala je na lokalnu izloženost inhibitoru kamenca od mjesta curenja udubljenja.Curenje je uzrokovano piting korozijom od strane visoko korozivne kemikalije i curenjem kroz liniju za ubrizgavanje kemikalija u proizvodno kućište.Inhibitor kamenca je raspršen iz kapilarne linije sa udubljenjem na kućište i cijev i došlo je do curenja.Bilo kakve sekundarne posljedice curenja u liniji za ubrizgavanje nisu uzete u obzir.Zaključeno je da je korozija kućišta i cijevi rezultat koncentriranih inhibitora kamenca koji se odvode od udubljene kapilarne linije na kućište i cijev, sl.5.
U ovom slučaju nije bilo angažovanja inženjera materijalne kompetencije.Korozivnost hemikalije na liniji DHCI nije testirana i sekundarni efekti zbog curenja nisu procenjeni;kao što je da li okolni materijali mogu tolerisati izlaganje hemikalijama.
Istorija slučaja kralja hemijskog oružja
Redoslijed događaja
Strategija prevencije kamenca za HP HT polje bila je kontinuirano ubrizgavanje inhibitora kamenca uzvodno od sigurnosnog ventila nizvodno.U bušotini je identifikovan ozbiljan potencijal stvaranja kamenca kalcijum karbonata.Jedan od izazova bila je visoka temperatura i visoke stope proizvodnje plina i kondenzata u kombinaciji sa niskom proizvodnjom vode.Zabrinutost zbog ubrizgavanja inhibitora kamenca bila je da bi se rastvarač odstranio zbog velike brzine proizvodnje gasa i da bi se hemikalija razvila na mestu ubrizgavanja uzvodno od sigurnosnog ventila u bušotini, sl.1.
Prilikom kvalifikacije inhibitora kamenca fokus je bio na efikasnosti proizvoda u HP HT uslovima uključujući ponašanje u sistemu gornjeg procesa (niska temperatura).Taloženje samog inhibitora kamenca u proizvodnim cijevima zbog velike količine plina bila je glavna briga.Laboratorijski testovi su pokazali da inhibitor kamenca može precipitirati i prianjati na zid cijevi.Zbog toga bi rad sigurnosnog ventila mogao smanjiti rizik.
Iskustvo je pokazalo da je nakon nekoliko sedmica rada kemijski vod curio.Bilo je moguće pratiti tlak u bušotini na površinskom mjeraču koji je instaliran u kapilarnoj liniji.Linija je izolirana da bi se postigao integritet bunara.
Linija za ubrizgavanje hemikalija je izvučena iz bunara, otvorena i pregledana kako bi se dijagnosticirao problem i pronašli mogući razlozi kvara.Kao što se može vidjeti na slici 6, pronađena je značajna količina precipitata i hemijska analiza je pokazala da je dio toga bio inhibitor kamenca.Precipitat se nalazio na zaptivci, a otvor i ventil nisu mogli raditi.
Otkazivanje ventila je uzrokovano krhotinama unutar sistema ventila koji su spriječili nepovratne ventile da progrizu sjedište od metala do metala.Krhotine su pregledane i pokazalo se da su glavne čestice metalne strugotine, vjerovatno nastale tokom procesa ugradnje kapilarne linije.Osim toga, neki bijeli ostaci su identificirani na oba nepovratna ventila, posebno na stražnjoj strani ventila.Ovo je strana niskog pritiska, tj. strana bi uvek bila u kontaktu sa fluidima bušotine.U početku se vjerovalo da se radi o krhotinama iz proizvodne bušotine jer su ventili bili zaglavljeni otvoreni i izloženi tekućinama iz bušotine.Ali ispitivanje krhotina pokazalo se da su polimeri sa sličnom hemijom kao i hemikalija koja se koristi kao inhibitor kamenca.Ovo nas je zainteresovalo i Statoil je želeo da istraži razloge koji stoje iza ovih polimernih ostataka prisutnih u kapilarnoj liniji.
Hemijska kvalifikacija
U području HP HT postoji mnogo izazova u pogledu odabira odgovarajućih kemikalija za ublažavanje različitih proizvodnih problema.U kvalifikaciji inhibitora kamenca za kontinuirano injektiranje u bušotini izvršena su sljedeća ispitivanja:
● Stabilnost proizvoda
● Termičko starenje
● Testovi dinamičkih performansi
● Kompatibilnost sa formacijskom vodom i inhibitorom hidrata (MEG)
● Statički i dinamički test kralja oružja
● Informacije o ponovnom rastvaranju voda, svježa kemikalija i MEG
Hemikalija će se ubrizgati unaprijed određenom dozom,ali proizvodnja vode neće nužno biti konstantna,tj. zalivanje vode.Između vodenih puževa,kada hemikalija uđe u bušotinu,dočekaće ga vruće,brza struja ugljovodoničnog gasa.Ovo je slično ubrizgavanju inhibitora kamenca u aplikaciju gas lifta (Fleming ital.2003). Zajedno sa
visoka temperatura gasa,Rizik od skidanja rastvarača je izuzetno visok i gun king može uzrokovati blokadu ventila za ubrizgavanje.Ovo je rizik čak i za hemikalije formulisane sa rastvaračima sa visokom tačkom ključanja/niskim pritiskom pare i drugim depresorima parnog pritiska (VPD). U slučaju delimičnog začepljenja,protok formacijske vode,MEG i/ili sveža hemikalija moraju biti u stanju da uklone ili ponovo rastvore dehidriranu ili ispuštenu hemikaliju.
U ovom slučaju, nova laboratorijska oprema za testiranje je dizajnirana da replicira uslove protoka u blizini injekcionih otvora na HP/HTg kao proizvodnom sistemu.Rezultati dinamičkih gun king testova pokazuju da je u predloženim uvjetima primjene zabilježen značajan gubitak rastvarača.To bi moglo dovesti do brzog "kinga" oružja i konačnog blokiranja dovodnih vodova.Rad je stoga pokazao da postoji relativno značajan rizik za kontinuirano ubrizgavanje hemikalija u ove bunare prije proizvodnje vode i doveo je do odluke da se prilagode normalne procedure pokretanja za ovo polje, odgađajući ubrizgavanje kemikalija dok se ne otkrije prodor vode.
Kvalifikacija inhibitora naslaga kamenca za kontinuirano injektiranje niz bušotine imala je veliki fokus na uklanjanju rastvarača i 'kingu' inhibitora kamenca na mjestu injektiranja i u dovodnoj liniji, ali nije procijenjen potencijal za stvaranje vode u samom ventilu za ubrizgavanje.Ventil za ubrizgavanje je vjerovatno otkazao zbog značajnog gubitka rastvarača i brzog kinga pištolja,Slika 6. Rezultati pokazuju da je važno imati holistički pogled na sistem;ne fokusirati se samo na izazove proizvodnje,ali i izazove u vezi sa ubrizgavanjem hemikalije,odnosno ventil za ubrizgavanje.
Iskustvo iz drugih oblasti
Jedan od ranih izvještaja o problemima s linijama za ubrizgavanje kemikalija na velikim udaljenostima bio je sa satelitskih polja Gull fak sandVig dis (Osa et al.2001). Podmorski injekcioni vodovi su blokirani od stvaranja hidrata unutar linije zbog invazije plina iz proizvedenih fluida u liniju preko ventila za ubrizgavanje.Izrađene su nove smjernice za razvoj podmorskih hemikalija za proizvodnju.Zahtjevi su uključivali uklanjanje čestica (filtraciju) i dodavanje inhibitora hidrata (npr. glikola) svim inhibitorima kamenca na bazi vode koji se ubrizgavaju u podmorske uzorke.Hemijska stabilnost,viskoznost i kompatibilnost (tečnost i materijali) su takođe uzeti u obzir.Ovi zahtjevi su dalje preuzeti u Statoil sistem i uključuju ubrizgavanje hemikalija u bušotinu.
Tokom faze razvoja Oseberg S ili polja odlučeno je da se sve bušotine završe sa DHC I sistemima (Fleming et al.2006). Cilj je bio spriječiti CaCO;skaliranje u gornjoj cijevi SI injekcijom.Jedan od najvećih izazova u pogledu linija za ubrizgavanje kemikalija bilo je postizanje komunikacije između površine i ispusta iz bušotine.Unutrašnji prečnik linije za ubrizgavanje hemikalija se suzio sa 7 mm na 0,7 mm (ID) oko sigurnosnog ventila prstena zbog ograničenja prostora i sposobnosti tečnosti da se transportuje kroz ovu sekciju uticali su na uspeh.Nekoliko platformskih bunara imalo je vodove za ubrizgavanje hemikalija koji su bili zapušeni,ali razlog nije bio shvaćen.Vlakovi raznih tečnosti (glikol,sirovo,kondenzat,ksilen,inhibitor kamenca,voda itd.) laboratorijski su testirani na viskoznost i kompatibilnost i pumpani naprijed i u obrnutom toku kako bi se otvorili vodovi;kako god,inhibitor ciljanog kamenca nije mogao da se pumpa sve do ventila za ubrizgavanje hemikalije.Dalje,komplikacije su uočene sa taloženjem fosfonatnog inhibitora kamenca zajedno sa zaostalom slanom otopinom CaCl z dovršetka u jednoj bušotini i puškom king inhibitora kamenca unutar bušotine s visokim omjerom plinskog ulja i niskim rezom vode (Fleming ital.2006)
Naučene lekcije
Razvoj metode ispitivanja
Glavne lekcije naučene iz kvara DHC I sistema su u pogledu tehničke efikasnosti inhibitora kamenca, a ne u pogledu funkcionalnosti i hemijskog ubrizgavanja.Injektiranje odozgo i podmorsko ubrizgavanje dobro su funkcionirale preko vremena;kako god,aplikacija je proširena na ubrizgavanje kemikalija u bušotinu bez odgovarajućeg ažuriranja metoda kemijske kvalifikacije.Statoilovo iskustvo iz dva prikazana slučaja na terenu je da se vodeća dokumentacija ili smjernice za kvalifikaciju hemikalija moraju ažurirati kako bi uključile ovu vrstu primjene hemikalija.Identifikovana su dva glavna izazova kao i) vakuum u liniji za ubrizgavanje hemikalija i ii) potencijalno taloženje hemikalije.
Do isparavanja hemikalije može doći na cijevi za proizvodnju (kao što se vidi u kućištu gun king) iu cijevi za ubrizgavanje (prelazna sučelja je identificirana u vakuumskom slučaju) postoji rizik da se ovi precipitati pomjere sa protokom i u injekcioni ventil i dalje u bunar.Ventil za ubrizgavanje je često dizajniran sa filterom uzvodno od tačke ubrizgavanja,ovo je izazov,jer u slučaju padavina ovaj filter može biti začepljen i ventil pokvari.
Opažanja i preliminarni zaključci iz naučenih lekcija rezultirali su opsežnom laboratorijskom studijom o fenomenima.Opšti cilj je bio razviti nove metode kvalifikacije kako bi se izbjegli slični problemi u budućnosti.U ovoj studiji provedena su različita ispitivanja i nekoliko laboratorijskih metoda je dizajnirano (razvijeno u cilju) za ispitivanje kemikalija s obzirom na identificirane izazove.
● Začepljenja filtera i stabilnost proizvoda u zatvorenim sistemima.
● Uticaj delimičnog gubitka rastvarača na korozivnost hemikalija.
● Uticaj delimičnog gubitka rastvarača unutar kapilare na formiranje čvrstih materija ili viskoznih čepova.
Tokom ispitivanja laboratorijskih metoda identifikovano je nekoliko potencijalnih problema
● Ponovljene blokade filtera i loša stabilnost.
● Formiranje čvrstih materija nakon delimičnog isparavanja iz kapilare
● PH promjene zbog gubitka rastvarača.
Priroda provedenih testova također je pružila dodatne informacije i znanja u vezi s promjenama fizičkih svojstava kemikalija unutar kapilara kada su podvrgnute određenim uvjetima,i kako se to razlikuje od rastvora u rasutom stanju pod sličnim uslovima.Testiranjem su također utvrđene značajne razlike između tečnosti u rasutom stanju,parne faze i rezidualne tečnosti koje mogu dovesti do povećanog potencijala za taloženje i/ili povećane korozivnosti.
Procedura ispitivanja korozivnosti inhibitora kamenca je razvijena i uključena u mjerodavnu dokumentaciju.Za svaku primjenu moralo se izvršiti prošireno ispitivanje korozivnosti prije nego što se može implementirati ubrizgavanje inhibitora kamenca.Također su obavljeni testovi hemikalije u liniji za ubrizgavanje.
Prije početka kvalifikacije hemikalije važno je stvoriti obim posla koji opisuje izazove i svrhu hemikalije.U početnoj fazi važno je identificirati glavne izazove kako biste mogli odabrati tip(e) kemikalija(e) koje će riješiti problem.Sažetak najvažnijih kriterijuma prihvatanja može se naći u tabeli 2.
Kvalifikacija hemikalija
Kvalifikacija hemikalija se sastoji od testiranja i teorijske evaluacije za svaku primenu.Tehnička specifikacija i kriteriji ispitivanja moraju biti definirani i uspostavljeni,na primjer u okviru HSE,kompatibilnost materijala,stabilnost proizvoda i kvaliteta proizvoda (čestice).Dalje,tačka smrzavanja,viskoznost i kompatibilnost sa drugim hemikalijama,inhibitor hidrata,moraju se odrediti formacijske vode i proizvedeni fluid.Pojednostavljena lista metoda ispitivanja koje se mogu koristiti za kvalifikaciju hemikalija data je u tabeli 2.
Kontinuirano fokusiranje i praćenje tehničke efikasnosti,brzine doziranja i HSE činjenice su važne.Zahtjevi proizvoda mogu promijeniti životni vijek polja ili procesnog postrojenja;variraju u zavisnosti od brzine proizvodnje kao i sastava tečnosti.Prateća aktivnost sa evaluacijom učinka,optimizacija i/ili testiranje novih hemikalija mora se raditi često kako bi se osigurao optimalan program tretmana.
U zavisnosti od kvaliteta ulja,proizvodnja vode i tehnički izazovi u proizvodnom pogonu na moru,upotreba proizvodnih hemikalija je možda neophodna za postizanje kvaliteta izvoza,regulatorni zahtjevi,i da upravljaju instalacijom na moru na siguran način.Sva polja imaju različite izazove, a potrebne hemikalije za proizvodnju će se razlikovati od polja do polja i prekovremenog rada.
Važno je fokusirati se na tehničku efikasnost proizvodnih hemikalija u kvalifikacionom programu,ali je takođe veoma važno fokusirati se na svojstva hemikalije,kao što je stabilnost,kvaliteta i kompatibilnost proizvoda.Kompatibilnost u ovoj postavci znači kompatibilnost sa tekućinama,materijala i drugih proizvodnih hemikalija.Ovo može biti izazov.Nije poželjno koristiti hemikaliju za rješavanje problema da bi se kasnije otkrilo da hemikalija doprinosi ili stvara nove izazove.Možda su svojstva hemikalije, a ne tehnički izazov koji je najveći izazov.
Posebni zahtjevi
Posebne zahtjeve za filtraciju isporučenih proizvoda treba primijeniti za podmorski sistem i za kontinuirano ubrizgavanje u bušotinu.Cjedila i filteri u sistemu za ubrizgavanje hemikalija treba da budu obezbeđeni na osnovu specifikacije opreme koja se nalazi nizvodno od gornjeg sistema za ubrizgavanje,pumpe i ventili za ubrizgavanje,na ventile za ubrizgavanje u bušotini.Kada se primenjuje kontinuirano ubrizgavanje hemikalija u bušotinu, specifikacija u sistemu za ubrizgavanje hemikalija treba da se zasniva na specifikaciji sa najvećom kritičnošću.Ovo je možda filter na injekcionom ventilu u donjoj rupi.
Izazovi ubrizgavanja
Sistem injektiranja može podrazumijevati 3-50 km udaljenosti pupčane podmorske linije i 1-3 km dolje u bunar.Važna su fizička svojstva kao što su viskoznost i sposobnost pumpanja hemikalija.Ako je viskoznost na temperaturi morskog dna previsoka, može biti izazov pumpati kemikaliju kroz vod za ubrizgavanje kemikalije u podmorski pupčani kanal i do podmorske točke ubrizgavanja ili u bušotinu.Viskoznost treba da bude u skladu sa specifikacijom sistema na očekivanoj temperaturi skladištenja ili radnoj temperaturi.Ovo treba procijeniti u svakom slučaju,i zavisiće od sistema.Kao sto je stopa ubrizgavanja hemikalija faktor uspeha u hemijskom ubrizgavanju.Da bi se smanjio rizik od začepljenja linije za ubrizgavanje hemikalija,hemikalije u ovom sistemu treba da budu inhibirane (ako postoji mogućnost hidratacije).Mora se izvršiti kompatibilnost sa tekućinama prisutnim u sistemu (tečnost za konzerviranje) i inhibitorom hidrata.Ispitivanje stabilnosti hemikalije na stvarnim temperaturama (najniža moguća temperatura okoline,temperatura okoline,temperatura podmorja,temperatura ubrizgavanja) moraju biti prođene.
Mora se uzeti u obzir i program za pranje vodova za ubrizgavanje hemikalija na datoj frekvenciji.Redovno ispiranje linije za ubrizgavanje hemikalija rastvaračem može dati preventivni efekat,glikol ili kemikalija za čišćenje za uklanjanje mogućih naslaga prije nego što se nakupe i mogu uzrokovati začepljenje linije.Odabrana hemijska otopina tekućine za ispiranje mora bitikompatibilan sa hemikalijom u liniji za ubrizgavanje.
U nekim slučajevima, linija za ubrizgavanje hemikalija se koristi za nekoliko hemijskih primena na osnovu različitih izazova tokom životnog veka polja i uslova fluida.U početnoj fazi proizvodnje prije prodora vode, glavni izazovi mogu biti drugačiji od onih u kasnom životnom vijeku koji su često povezani sa povećanom proizvodnjom vode.Prelazak sa inhibitora na bazi rastvarača bez vode, kao što je inhibitor asfaltena, na hemikalije na bazi vode, kao što je inhibitor kamenca, može predstavljati izazove sa kompatibilnošću.Stoga je važno fokusirati se na kompatibilnost i kvalifikaciju i upotrebu odstojnika kada se planira izmjena hemikalije u liniji za ubrizgavanje hemikalija.
Materijali
Što se tiče kompatibilnosti materijala,sve hemikalije treba da budu kompatibilne sa brtvama,elastomeri,zaptivke i građevinski materijali koji se koriste u sistemu za ubrizgavanje hemikalija i proizvodnom pogonu.Treba razviti proceduru ispitivanja korozivnosti hemikalija (npr. inhibitor kiselog kamenca) za kontinuirano ubrizgavanje u bušotinu.Za svaku primjenu mora se obaviti prošireno ispitivanje korozivnosti prije nego što se može implementirati ubrizgavanje hemikalija.
Diskusija
Treba procijeniti prednosti i nedostatke kontinuiranog ubrizgavanja kemikalija u bušotinu.Kontinuirano ubrizgavanje inhibitora kamenca za zaštitu DHS Vor proizvodne cijevi je elegantna metoda zaštite bunara od kamenca.Kao što je spomenuto u ovom radu, postoji nekoliko izazova s kontinuiranim ubrizgavanjem kemikalija u bušotinu,međutim za smanjenje rizika važno je razumjeti fenomene povezane s rješenjem.
Jedan od načina da se smanji rizik je fokusiranje na razvoj metode ispitivanja.U poređenju sa gornjim ili podmorskim ubrizgavanjem hemikalija, postoje različiti i teži uslovi dole u bušotini.Procedura kvalifikacije hemikalija za kontinuirano ubrizgavanje hemikalija u bušotinu mora uzeti u obzir ove promjene uslova.Kvalifikacija hemikalija mora se vršiti prema materijalu sa kojim hemikalije mogu doći u kontakt.Zahtjevi za kvalifikaciju kompatibilnosti i testiranje u uvjetima koji repliciraju što je moguće bliže različitim uvjetima životnog ciklusa bušotine pod kojima će ovi sistemi raditi moraju se ažurirati i implementirati.Razvoj metode ispitivanja mora se dalje razvijati do realističnijih i reprezentativnijih testova.
Osim toga,interakcija između hemikalija i opreme je ključna za uspjeh.Razvoj hemijskih ventila za ubrizgavanje mora uzeti u obzir hemijska svojstva i lokaciju injekcionog ventila u bušotini.Trebalo bi razmotriti uključivanje pravih ventila za ubrizgavanje kao dio opreme za ispitivanje i provođenje testiranja performansi inhibitora kamenca i dizajna ventila kao dio programa kvalifikacije.Za kvalifikaciju inhibitora kamenca,glavni fokus je ranije bio na izazovima procesa i inhibiciji obima,ali dobra inhibicija kamenca zavisi od stabilnog i kontinuiranog ubrizgavanja.Bez stabilnog i kontinuiranog ubrizgavanja potencijal za kamenac će se povećati.Ako je ventil za ubrizgavanje inhibitora kamenca zagušen i nema ubrizgavanja inhibitora kamenca u tok tekućine,bunar i sigurnosni ventili nisu zaštićeni od kamenca i stoga bi sigurna proizvodnja mogla biti ugrožena.Kvalifikaciona procedura mora da vodi računa o izazovima vezanim za ubrizgavanje inhibitora kamenca pored izazova procesa i efikasnosti kvalifikovanog inhibitora kamenca.
Novi pristup uključuje nekoliko disciplina i saradnja između disciplina i odgovarajuće odgovornosti moraju biti razjašnjene.U ovoj aplikaciji gornji procesni sistem,uključeni su podmorski predlošci i projektiranje i završetak bušotina.Multidisciplinarne mreže koje se fokusiraju na razvoj robusnih rješenja za sisteme za ubrizgavanje kemikalija su važne i možda put do uspjeha.Komunikacija između različitih disciplina je kritična;Posebno je važna bliska komunikacija između hemičara koji imaju kontrolu nad hemikalijama koje se primenjuju i inženjera bunara koji imaju kontrolu nad opremom koja se koristi u bušotini.Razumjeti izazove različitih disciplina i učiti jedni od drugih je ključno za razumijevanje složenosti cijelog procesa.
Zaključak
● Kontinuirano ubrizgavanje inhibitora kamenca za zaštitu DHS Vor proizvodne cijevi su elegantna metoda za zaštitu bunara od kamenca
● Za rješavanje identificiranih izazova,sljedeće preporuke su:
● Mora se izvršiti posebna DHCI procedura kvalifikacije.
● Metoda kvalifikacije za ventile za ubrizgavanje kemikalija
● Metode ispitivanja i kvalifikacije za hemijsku funkcionalnost
● Razvoj metode
● Ispitivanje relevantnog materijala
● Multidisciplinarna interakcija u kojoj je komunikacija između različitih uključenih disciplina ključna za uspjeh.
Priznanja
Autor se želi zahvaliti Statoil AS A na dozvoli za objavljivanje ovog rada i Baker Hughesu i Schlumbergeru što su dozvolili korištenje slike na slici 2.
Nomenklatura
(Ba/Sr)SO4=barijum/stroncijum sulfat
CaCO3=kalcijum karbonat
DHCI = ubrizgavanje hemikalije u bušotini
DHSV=ispustni sigurnosni ventil
npr.=na primjer
GOR=odnos gasa
HSE=zdravstveno-bezbedno okruženje
HPHT=visoki pritisak visoka temperatura
ID=unutrašnji prečnik
tj=to jest
km=kilometri
mm=milimetar
MEG=mono etilen glikol
mMD=metar izmjerene dubine
OD=spoljni prečnik
SI = inhibitor skale
mTV D=metar ukupna vertikalna dubina
U-cijev = cijev u obliku slova U
VPD=sredstvo za smanjenje pritiska pare
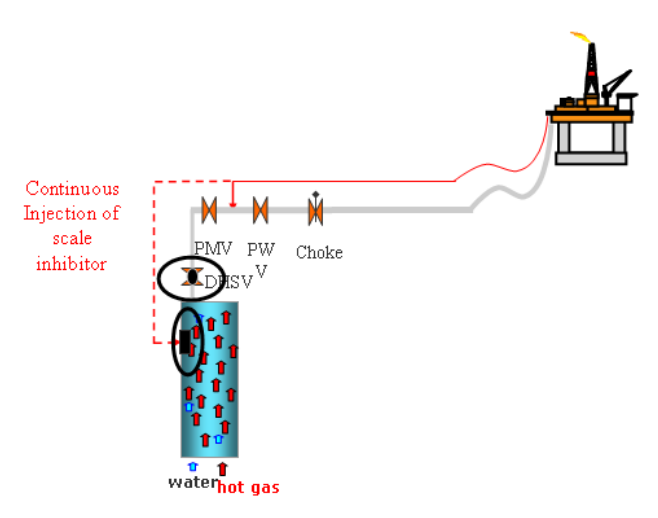
Slika 1. Pregled podmorskih i dubinskih sistema za ubrizgavanje kemikalija u atipičnom polju.Skica hemijskog ubrizgavanja uzvodno DHSV i povezani očekivani izazovi.DHS V = sigurnosni ventil u bušotini, PWV = krilni ventil procesa i PM V = glavni ventil procesa.
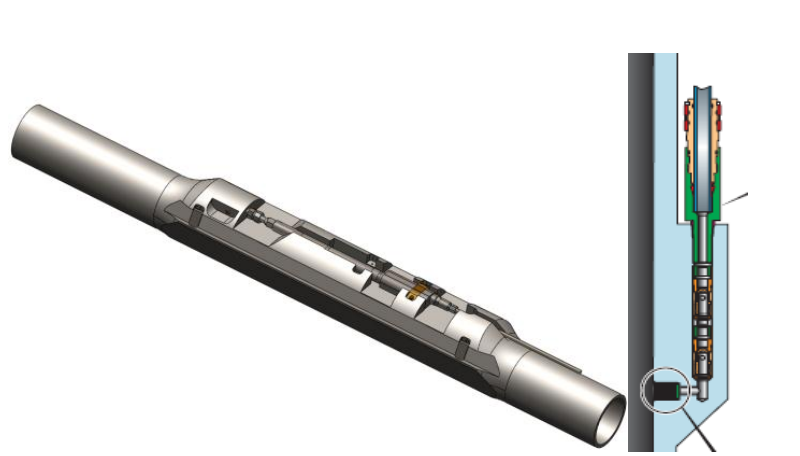
Slika 2. Skica atipičnog sistema za ubrizgavanje hemikalija u bušotinu sa trnom i ventilom.Sistem je spojen na površinski razvodnik, napajan kroz njega i spojen na vješalicu cijevi na prstenastoj strani cijevi.Trn za injektiranje hemikalija se tradicionalno postavlja duboko u bušotinu sa namerom da obezbedi hemijsku zaštitu.
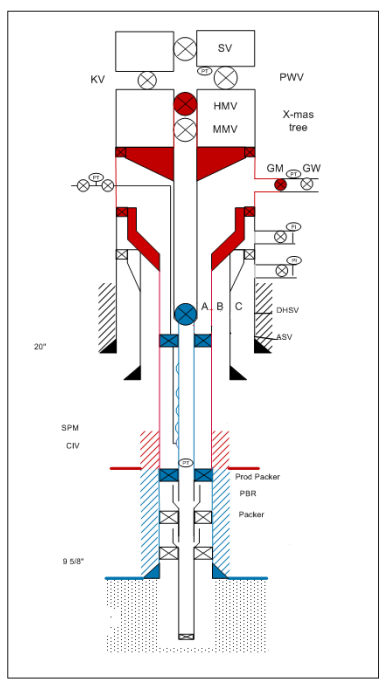
Slika 3. Šema tipične barijere bunara,gdje plava boja predstavlja primarni omotač barijere bunara;u ovom slučaju proizvodne cijevi.Crvena boja predstavlja omotač sekundarne barijere;kućište.Na lijevoj strani je naznačeno ubrizgavanje kemikalije, crna linija sa točkom ubrizgavanja do proizvodne cijevi u području označenom crvenom (sekundarna barijera).
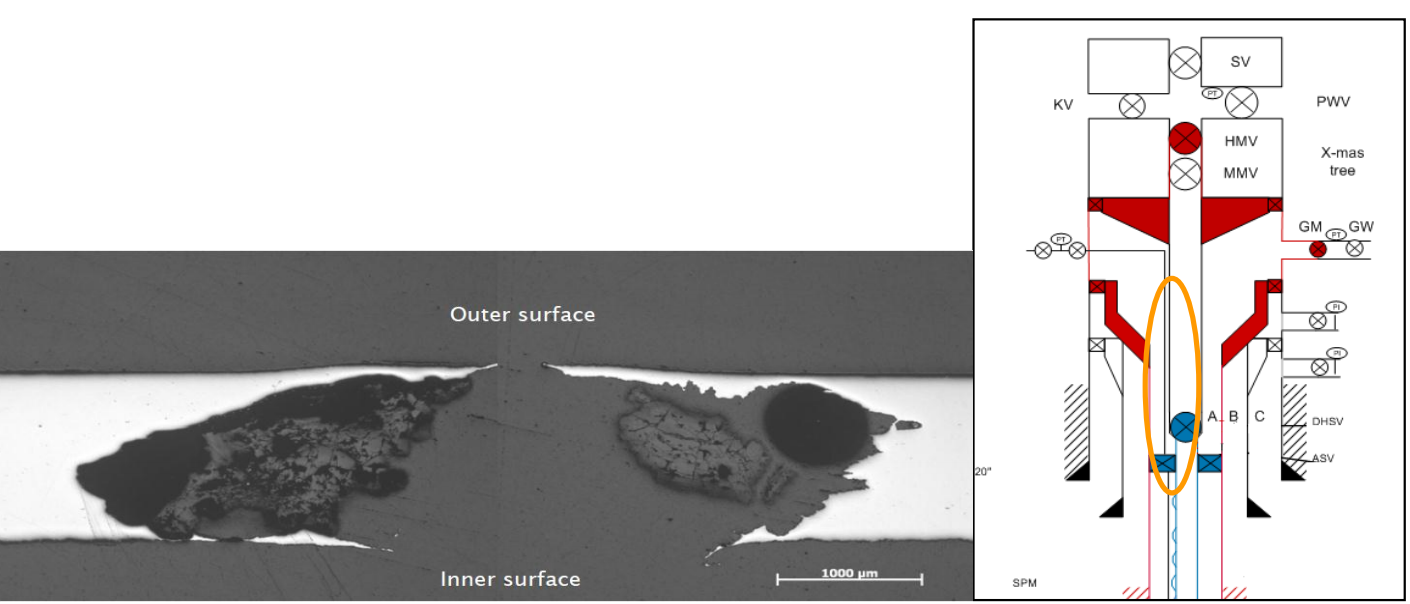
Slika 4. Rupa sa udubljenjem pronađena u gornjem dijelu linije za ubrizgavanje 3/8”.Područje je prikazano na skici šeme atipične barijere bunara, označeno narandžastom elipsom.
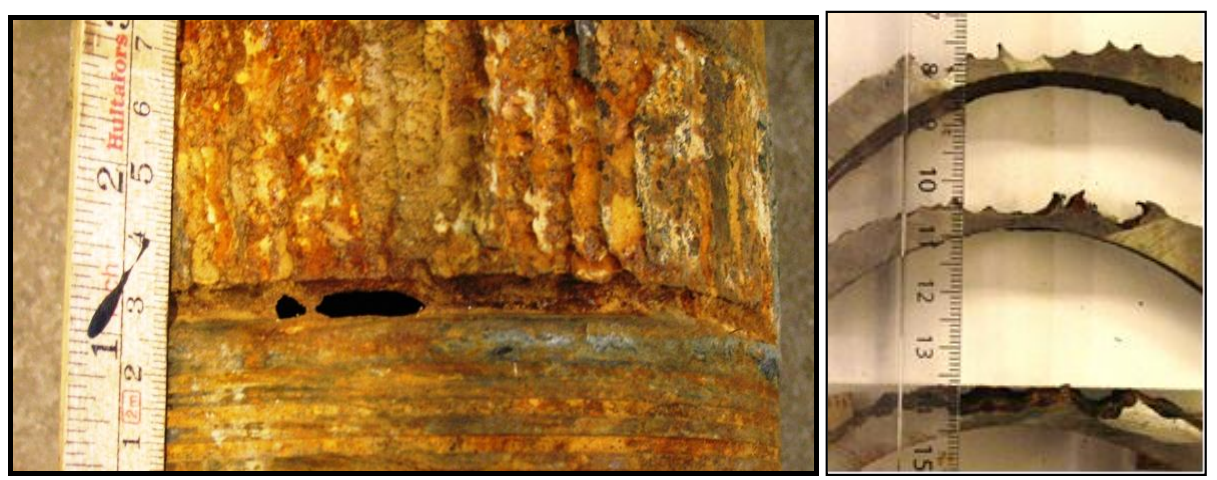
Slika 5. Teški napad korozije na 7” 3% Chrome cijevi.Slika prikazuje napad korozije nakon što je inhibitor kamenca raspršen iz linije za ubrizgavanje hemikalija sa udubljenjem na proizvodnu cijev.
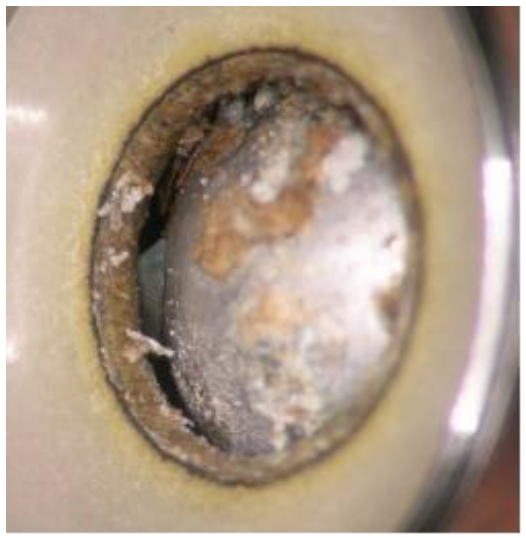
Slika 6. Krhotine pronađene u ventilu za ubrizgavanje kemikalija.Krhotine u ovom slučaju bile su metalne strugotine vjerovatno od procesa instalacije uz nešto bjelkastih krhotina.Ispitivanje bijelih krhotina pokazalo se da su polimeri sa sličnom hemijom kao i ubrizgana kemikalija
Vrijeme objave: Apr-27-2022